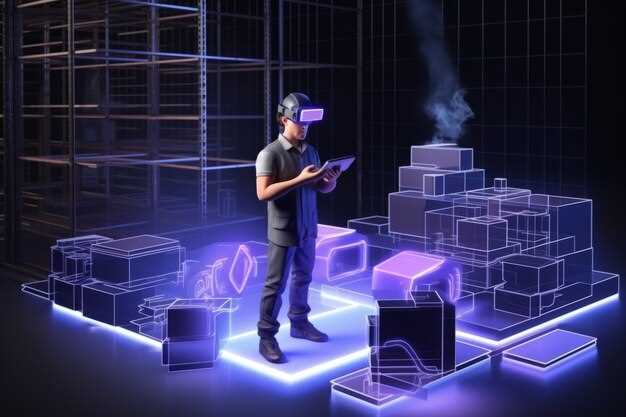
Implementing augmented reality (AR) can dramatically enhance productivity and accuracy in manufacturing. Companies adopting AR tools experience quicker training processes, where employees interact with digital overlays that provide real-time information and guidance on equipment and procedures. For instance, technicians equipped with AR glasses can follow step-by-step instructions displayed directly onto machinery, streamlining tasks and reducing the likelihood of errors.
Consider integrating AR into routine maintenance checks. AR applications can highlight critical components, offering visual cues and updates on the equipment’s status. This immediate access to data not only speeds up repairs but also minimizes downtime, which translates to significant cost savings. Research shows that businesses utilizing AR in maintenance see a reduction in errors by up to 30%.
Embrace AR solutions for remote collaboration as well. Engineers and specialists from various locations can connect through AR, allowing them to “see” the same workspace and provide real-time support. This collaboration tool leads to faster problem resolution, with studies indicating a 25% improvement in response times for troubleshooting issues.
Lastly, invest in employee engagement through AR-driven training programs. Interactive simulations enhance retention of complex information, leading to a more skilled workforce. Data suggests that training programs incorporating AR result in a 70% faster learning curve compared to traditional methods. By prioritizing AR technology, manufacturers can position themselves at the forefront of industry innovation.
Enhancing Equipment Maintenance with AR Tools
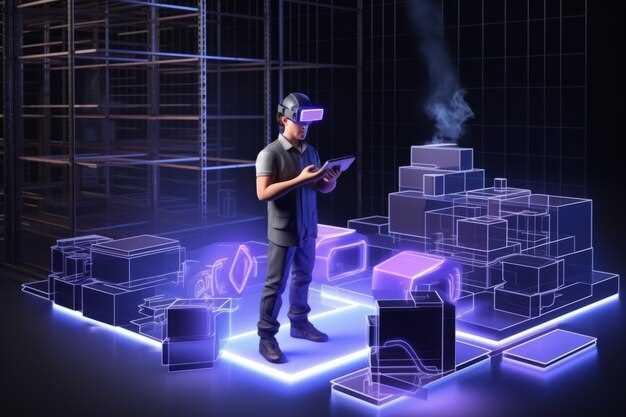
Utilize augmented reality (AR) tools to streamline equipment maintenance and reduce downtime. AR applications provide real-time visual guidance for technicians during repair processes. By overlaying step-by-step instructions directly onto the equipment, workers can address issues quickly and confidently.
Real-Time Data Access
Integrate AR with your existing maintenance management systems to offer technicians real-time access to equipment performance data. Display critical metrics such as temperature, pressure, and operating hours through AR glasses or mobile devices. This information helps identify potential problems before they lead to failures, allowing for proactive maintenance.
Training and Skill Development
Implement AR solutions for training new employees. Use interactive simulations that replicate real equipment scenarios. This hands-on approach shortens the learning curve and enhances retention. Experienced technicians can create AR content, sharing expertise and ensuring consistency in maintenance procedures across the workforce.
Implementing Remote Assistance to Streamline Production
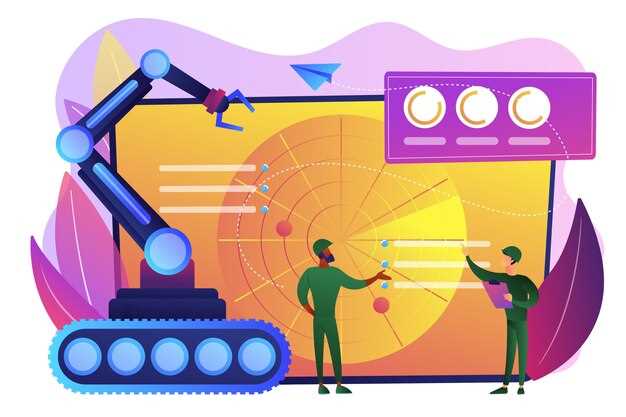
Use Augmented Reality (AR) tools to provide remote assistance for frontline workers. By integrating AR with video support, technicians can receive real-time guidance from experts, helping them resolve issues faster. This setup reduces downtime and minimizes the need for on-site visits, considerably cutting costs.
Deploy smart glasses equipped with AR capabilities. These devices allow workers to share their perspective live, enabling remote specialists to annotate visuals and highlight important steps. This hands-on approach enhances understanding and reduces training time, leading to quicker problem resolution.
Training and Implementation
Establish a structured training program for your team. Start with familiarization sessions on using AR devices and software, focusing on practical applications in daily tasks. Encourage feedback throughout the training to optimize the learning process and build confidence in using the technology. Additionally, develop a troubleshooting guide that workers can refer to during initial implementation.
Monitor adoption rates and gather performance metrics. Analyze how much time remote assistance saves and assess user satisfaction. By comparing these metrics against your production goals, you can identify areas for improvement and further refine the assistance program.
Collaboration and Continuous Improvement
Create a feedback loop between the on-site teams and remote experts. Regularly schedule meetings to discuss challenges experienced with the AR tools and levels of received support. Adjust training and resources based on this input, ensuring that remote assistance continuously evolves to meet production needs.
Incorporate cloud-based systems to store training materials and support documents. This creates a centralized knowledge base accessible to all personnel, facilitating ongoing learning and development. As employees become more adept at using AR for remote assistance, production efficiency and quality of work will improve significantly.
Transitioning to remote assistance using AR technologies marks a significant step towards modernizing production processes. By investing in the right tools and fostering a culture of collaboration and continuous learning, businesses set themselves up for sustained success in a competitive landscape.
Integrating AR into the Manufacturing Workflow
Implement AR technology to enhance training processes for operators. Hands-on training with augmented reality enhances understanding and retention. Employees can visualize complex machinery and processes, significantly reducing the learning curve.
Incorporate AR guidance in assembly lines. Overlaying digital instructions on physical components saves time and minimizes errors. Workers receive real-time feedback, ensuring tasks are performed correctly the first time.
Utilize AR for maintenance and repair tasks. Technicians equipped with AR glasses can view schematics and receive step-by-step instructions while working on equipment. This increases accuracy and reduces downtime, allowing for rapid troubleshooting.
Integrate AR into quality control processes. Use augmented reality to compare product dimensions and specifications against digital models. Instantly identify defects or deviations, helping maintain product integrity and adhere to quality standards.
Leverage AR for supply chain management. Visualize inventory levels, track shipments in real-time, and manage stock efficiently through AR applications. Streamlining these processes enhances decision-making and resource allocation.
Implement collaboration tools featuring AR capabilities. Virtual meetings with multi-user AR support enable spatial understanding of design or problem-solving sessions. Engage remote teams effectively, ensuring cohesive communication and collaboration.
Regularly evaluate AR’s impact on productivity and efficiency. Collect data on process improvements and operational savings. Use this information to refine AR applications and maximize their benefits within your manufacturing environment.
Utilizing Industrial AR for Operator Training
Integrate Augmented Reality (AR) into your operator training program to enhance learning outcomes. Use AR glasses or mobile devices to provide real-time guidance through visual overlays. This allows operators to interact with machinery in a simulated environment, reducing onboarding time and minimizing errors.
Key Techniques for Implementing AR in Training
- Hands-On Simulations: Create AR-based scenarios that mimic real operational tasks. Operators can practice skills without risking equipment damage or safety hazards.
- Step-by-Step Instructions: Overlay instructions directly onto machinery. This visual aid helps operators understand complex processes by following prompts visually during operation.
- Performance Tracking: Monitor progress through analytics integrated within the AR system. Analyze data on time taken for tasks or the number of mistakes made to tailor future training sessions.
Benefits of AR in Operator Training
- Improved Retention: Visual and interactive elements facilitate memory retention compared to traditional training methods.
- Customization: Tailor training content to specific roles or equipment, ensuring relevant learning experiences for all operators.
- Accelerated Learning: Reduce the time required to train new operators, enabling quicker integration into the workforce.
Encourage collaboration by incorporating AR into team training sessions, where operators can share insights and troubleshoot together. Engage employees by making the training sessions more dynamic and less monotonous.
Regularly update training content to reflect new equipment or procedures, ensuring continuous improvement in operator skills. This commitment to knowledge retention through AR can lead to higher productivity and reduced downtime.
Improving Quality Control Processes through AR Solutions
Integrate augmented reality (AR) solutions to enhance quality control through real-time data visualization and interactive procedures. Utilize AR to project essential metrics and specifications directly onto the product, making it easy for inspectors to identify deviations instantly.
Implement AR glasses or mobile applications that guide workers through inspection processes step-by-step. This reduces training time and minimizes human error. For instance, AR can overlay images of defect-free products, enabling inspectors to quickly compare and determine quality conformance.
Incorporate AR into existing quality management systems. Link AR applications to databases and analytics tools to provide an instant view of historical performance data. It allows for informed decision-making based on trends and quality metrics, promoting continuous improvement.
Enhance communication across teams using AR for virtual meetings during inspections. Remote experts can guide on-site staff, improving skills and reducing the need for travel. This collaboration streamlines problem resolution and reduces downtime associated with quality issues.
Leverage AR for predictive maintenance as part of quality assurance. By analyzing data from equipment sensors, AR can help identify potential issues before they lead to defects, maintaining product quality and extending machinery lifespan.
Conduct regular audits of AR-supported processes to ensure alignment with quality standards and to identify areas for enhancement. Feedback from users will help refine AR applications, making them more intuitive and effective in real-world scenarios.
Invest in AR training sessions for quality control staff to maximize tool effectiveness. Understanding the technology deeply leads to higher confidence and better results in inspections.
By adopting AR solutions in quality control, organizations can achieve higher accuracy, improve operational efficiency, and enhance overall product quality. Start exploring AR tools tailored for your quality control needs today.
Augmented Reality for Safety Training in Manufacturing Environments
Utilize augmented reality (AR) for immersive safety training sessions in manufacturing. By integrating AR, you allow trainees to experience real-life scenarios without physical risk. This approach enhances understanding and retention of safety protocols.
Implement AR simulations that replicate hazardous situations, enabling workers to practice their responses. For example, employ AR to visualize equipment malfunctions or emergency evacuations in a 3D space. This hands-on experience prepares employees for genuine challenges encountered on-site.
Leverage AR-enabled devices, such as smart glasses and mobile applications, to deliver interactive content. This technology can project safety guidelines, highlight danger zones, and provide step-by-step instructions for handling machinery.
Below is a table summarizing key benefits of using AR in safety training:
Benefits | Description |
---|---|
Real-World Scenarios | Simulate realistic conditions for better preparedness. |
Lower Training Costs | Reduce expenses by minimizing physical materials and equipment needed for training. |
Increased Engagement | Interactive learning keeps employees focused and motivated. |
Instant Feedback | Allow trainees to receive immediate tips and corrections during practice. |
Accessibility | Provide training resources at any time and place, ensuring all employees can participate. |
Continuously update AR training modules based on new safety regulations and feedback from employees. This ensures relevance and effectiveness in keeping the workforce informed about the latest safety practices.
Encourage collaboration among staff during AR training sessions to cultivate a culture of safety awareness. Engage employees in discussions regarding challenges and best practices observed during their training experiences.
Investing in AR for safety training pays off in reduced accidents and increased confidence among workers. Prioritize sustainable training approaches to enhance workplace safety continually. With AR, training becomes not just more effective but also a proactive measure that benefits the entire organization.
Case Studies of Successful AR Deployments in Industry
Starting with Boeing, the aerospace manufacturer has integrated augmented reality into its assembly processes. Technicians use AR glasses to view 3D wiring diagrams overlaid on actual aircraft parts. This approach decreased assembly errors by 40% and reduced the time needed for assembly by 35%. The glasses provide real-time feedback, allowing workers to make adjustments on the fly.
Next, Siemens has implemented AR in their production facilities, specifically for maintenance tasks. Technicians equipped with AR tools can view step-by-step repair instructions directly on machinery, which improved repair time by 20%. This deployment enhances collaboration, enabling remote experts to guide technicians through complex repairs using live video feeds and AR annotations.
Volkswagen has also utilized AR to streamline training processes for new employees. They created immersive simulations that allow workers to experience assembly line tasks in a risk-free environment. This initiative shortened the onboarding time for new hires by 30%, ensuring they can become productive team members sooner.
- Boeing: AR glasses for aircraft assembly; 40% reduction in errors.
- Siemens: AR tools for maintenance; 20% improvement in repair speed.
- Volkswagen: Immersive AR training; 30% faster onboarding for new employees.
Furthermore, General Electric (GE) employs AR in their turbine manufacturing process. Workers use AR devices to project work instructions and safety guidelines directly onto the components they’re handling. This practice has led to a significant reduction in accidents and improved compliance with safety protocols.
In the automotive industry, Ford has adopted AR applications for product design and development. Virtual prototypes allow designers to visualize changes instantly, resulting in a quicker design iteration process. This method shortened development time by 25%, enabling faster time-to-market for new models.
- General Electric: Projected work instructions enhance safety in turbine manufacturing.
- Ford: AR in design; 25% reduction in product development time.
These case studies illustrate the tangible benefits of AR in manufacturing and industrial applications. Focus on integrating AR tools tailored to specific operational needs to achieve similar results. Efforts should emphasize training, maintenance, and design optimization to enhance productivity and safety across various sectors.
Future Trends in AR Technology for Manufacturing
Integrating AR technology with AI and machine learning creates adaptive systems that learn from manufacturing processes, optimizing workflows and predictive maintenance. These systems analyze data in real-time, adjusting parameters to enhance production efficiency. Companies should invest in training employees to utilize these technologies effectively, ensuring a seamless transition to advanced systems.
Remote Collaboration and Support
AR facilitates remote collaboration, allowing technicians to assist with equipment malfunctions through interactive visual guides. By leveraging AR glasses or apps, experts can view real-time data and give instructions during repairs. Manufacturers should consider adopting these technologies to reduce downtime and enhance service quality. Regular training on AR tools will empower teams to leverage this feature efficiently.
Sustainability and Resource Management
AR applications support sustainability by optimizing resource management. By visualizing energy consumption and material waste, manufacturers can pinpoint areas for improvement. Companies can attain significant savings by adopting AR solutions that promote sustainable practices. Tracking these improvements will not only benefit the environment but also bolster corporate responsibility initiatives.
Video:
Industrial Augmented Reality – Aircada Pro
Industrial Augmented Reality – Aircada Pro by Aircada Pro 7,532 views 2 years ago 2 minutes, 40 seconds
Q&A:
What are the main benefits of using augmented reality in manufacturing?
Using augmented reality (AR) in manufacturing brings several significant advantages. Firstly, it enhances training by providing workers with interactive guidance, which allows them to learn processes more quickly and effectively. Secondly, AR can improve maintenance procedures by overlaying digital information onto physical equipment, helping technicians to identify issues and execute repairs with better precision. This technology also aids in design and prototyping, allowing teams to visualize components and processes in real-time, which can lead to increased innovation and reduced time-to-market. Lastly, AR can facilitate better collaboration among teams, as remote experts can assist on-site workers through real-time visual instructions.
How does augmented reality impact worker safety in industrial environments?
Augmented reality significantly enhances worker safety in various ways. By providing real-time data and instructions, AR can help workers be more aware of their surroundings and potential hazards. For instance, AR can highlight safety equipment in use or alert workers to dangerous areas in a facility. Additionally, AR training programs can simulate hazardous situations without any real-world risk, allowing employees to practice their responses. This proactive approach to safety can lead to reduced accidents and a better understanding of safety protocols among employees, ultimately creating a safer work environment.
What challenges do companies face when implementing augmented reality in manufacturing?
Implementing augmented reality in manufacturing comes with several challenges. One significant hurdle is the initial investment in AR technology, including hardware, software, and training. Integration with existing systems can be complex, requiring careful planning and execution. Additionally, there may be resistance from employees who are unfamiliar with the technology or who fear that it may replace their jobs. Finally, ensuring data security and privacy when using AR applications is critical, as sensitive information can be vulnerable to cyber threats. Companies must address these challenges through comprehensive training, a phased implementation approach, and stringent security measures.
Can augmented reality be used in remote support for manufacturing processes?
Yes, augmented reality is highly effective for remote support in manufacturing processes. It allows technicians in different locations to collaborate in real time. For example, an expert can use AR to guide a technician through complex repairs by overlaying instructions and diagrams directly onto the equipment being worked on. This not only reduces downtime but also minimizes the need for travel, cut costs, and speeds up response times. Remote support through AR enhances problem-solving efficiency, helping teams to tackle issues quickly and effectively.
What industries outside of manufacturing can benefit from augmented reality technology?
Many industries beyond manufacturing can benefit from augmented reality technology. In healthcare, AR can assist surgeons through enhanced visualization during procedures. The retail sector can use AR to create immersive shopping experiences, allowing customers to visualize products in their environment. Education can leverage AR for interactive learning experiences, making complex subjects more engaging. Additionally, architecture and construction can utilize AR for visual inspections and project visualization, assisting in better planning and execution of projects. Overall, AR has widespread applications, enhancing innovation and efficiency across various sectors.
What are the main benefits of using augmented reality (AR) in manufacturing?
Using augmented reality in manufacturing offers several key advantages. Firstly, it enhances training and onboarding processes for new employees. AR provides interactive, visual instructions that can simplify complex tasks, making it easier for workers to learn machinery operation or assembly processes. Secondly, AR can improve maintenance procedures by overlaying digital information on physical equipment, allowing technicians to diagnose issues more efficiently and accurately. Thirdly, AR facilitates remote collaboration, enabling experts to assist on-site workers in real-time, reducing downtime and travel costs. Additionally, AR can boost productivity by streamlining workflows and minimizing errors, ultimately leading to improved overall quality and reduced operational costs.